Workshop
The differences in sound and function of classical and flamenco guitars are enormous. The colour spectrum, response, dynamic range, balance, loudness, and projection are some of the variables that distinguish them. How are these achieved, and how can specific ideas be realised?
Acoustically treated the guitar forms a coupled oscillation system. The finger plucks the string and initiates the string vibration, this causes the neck and bridge/top vibration, and this in turn sets the surrounding air at the interior and exterior of the top into movement. Plate oscillations (top, back, sides), air chamber vibration (Helmholtz resonant frequency and others), string oscillations, and the resonant frequencies of each single component (braces, bars, linings, etc.) influence and interfere with each other in a favourable or unfavourable manner.
A complicating factor is that the guitar as a polyphonic instrument should have the capacity to project up to 6 tones, fundamentals and harmonics, evenly at the same time with only a single energy pulse per tone, the strike of the finger (compared with this a violin e.g. has to excite a maximum of 2 tones at the same time, with the help of a bow which can produce a permanent energy pulse).
In order to meet these unique requirements guitar construction concentrates mainly on three areas, the selection and tuning of the wood, construction design, and methodology. Each area contains an enormous number of parameters and possibilities, and because of the coupling every change in detail can lead to an immense change as a whole.
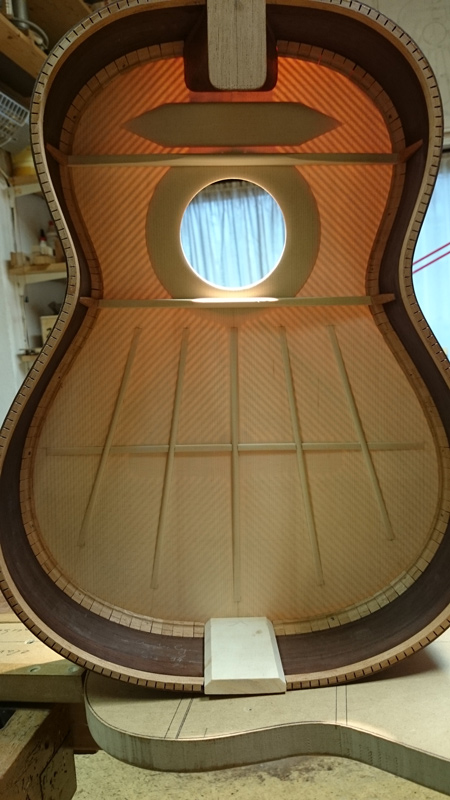
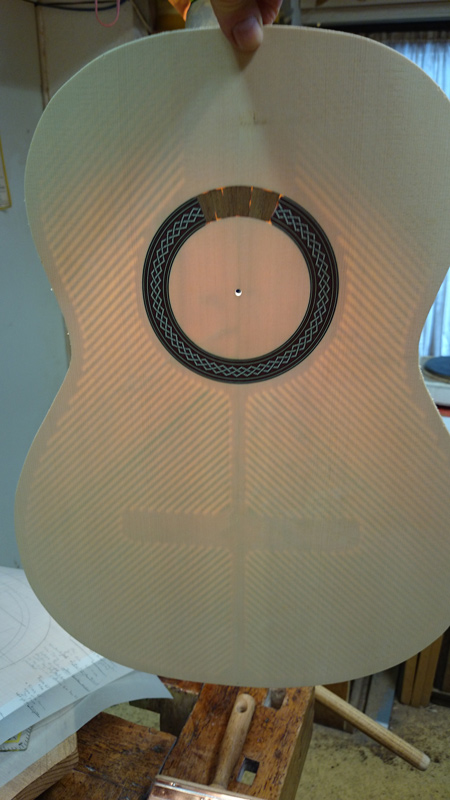
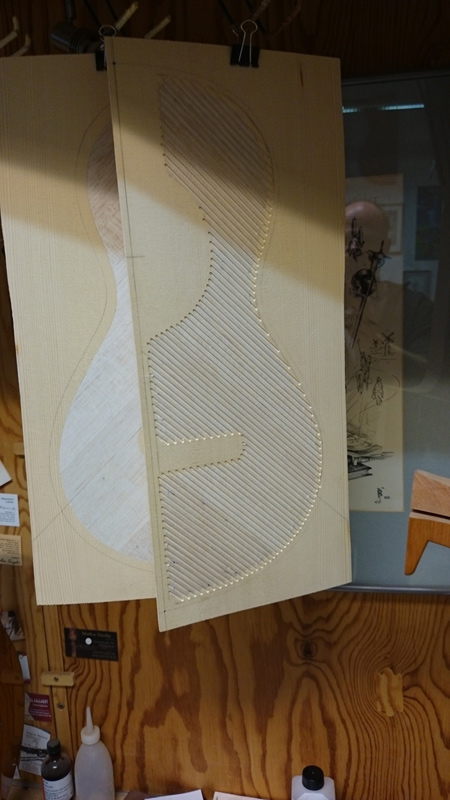
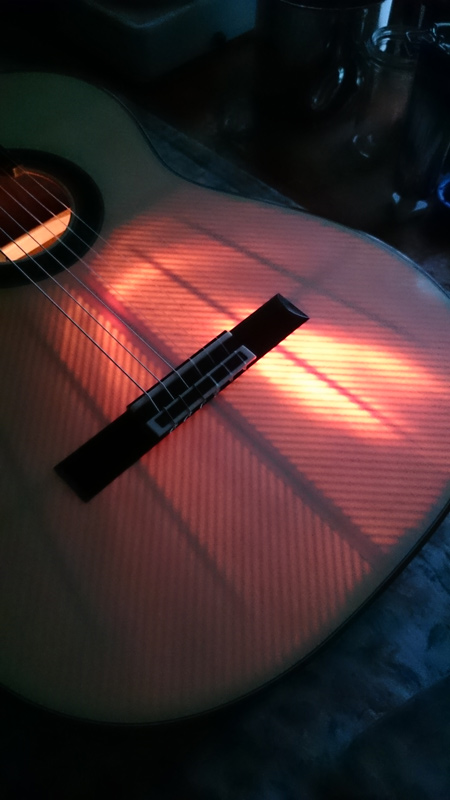
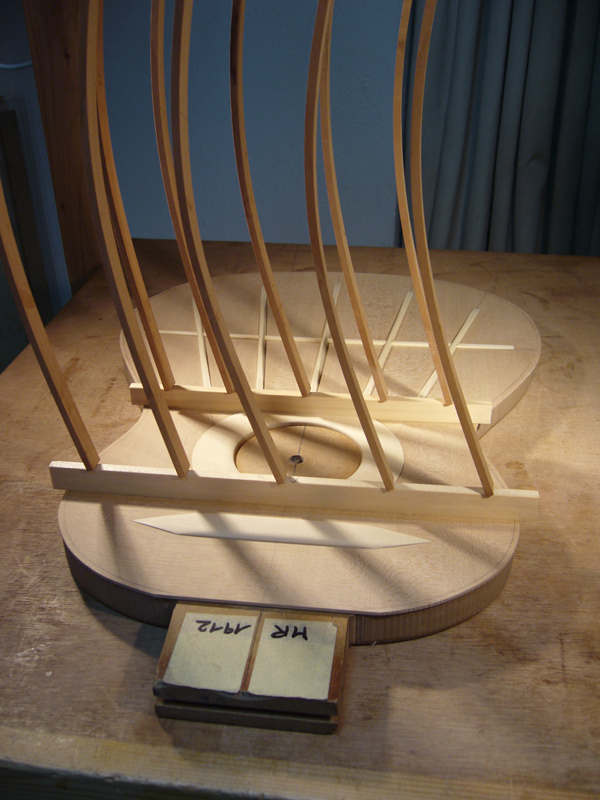
About Wood Selection
Where and how quickly a tree grows, when it is felled, how it is sawn, seasoned, and dried all contribute to the quality and suitability of its wood. Since each piece of wood is unique, it is clear that rather than adhering to a fixed building plan, the guitar’s variable dimensions, patterns, and methods must be in congruence for each instrument.
About Construction
The parts that make up the guitar body: soundboard, back, and sides are only 2 to 3 mm thick, but must withstand a string load of about 40 kilogram. For that reason guitar builders of the past have applied a myriad of static principles to their work in order to combine optimal vibrational freedom with stability and durability.
For that reason guitar builders of the past have applied a myriad of static principles to their work in order to combine optimal vibrational freedom with stability and durability. These include for example internal strutting, arched surfaces, and deliberate prestresses. The ideas and concepts are amazingly varied and naturally produce a wide range of results.
About Methodology
What especially fascinates me is the lively sound characteristic of many guitars from Southern Spain. Aside from wood selection and design it is mainly construction methods that influence this sound.
There exist a great number of possible ways to fashion and glue together the 40 to 50 pieces which comprise a guitar. Each of these in combination results in a unique system which affects the statics, and with it the sound.
Over generations builders have developed assembly methods very finely tuned to the instrument. This methodology harmonises perfectly with the use of hide and bone glues and shellac polish to form the basics of traditional Spanish guitar construction.
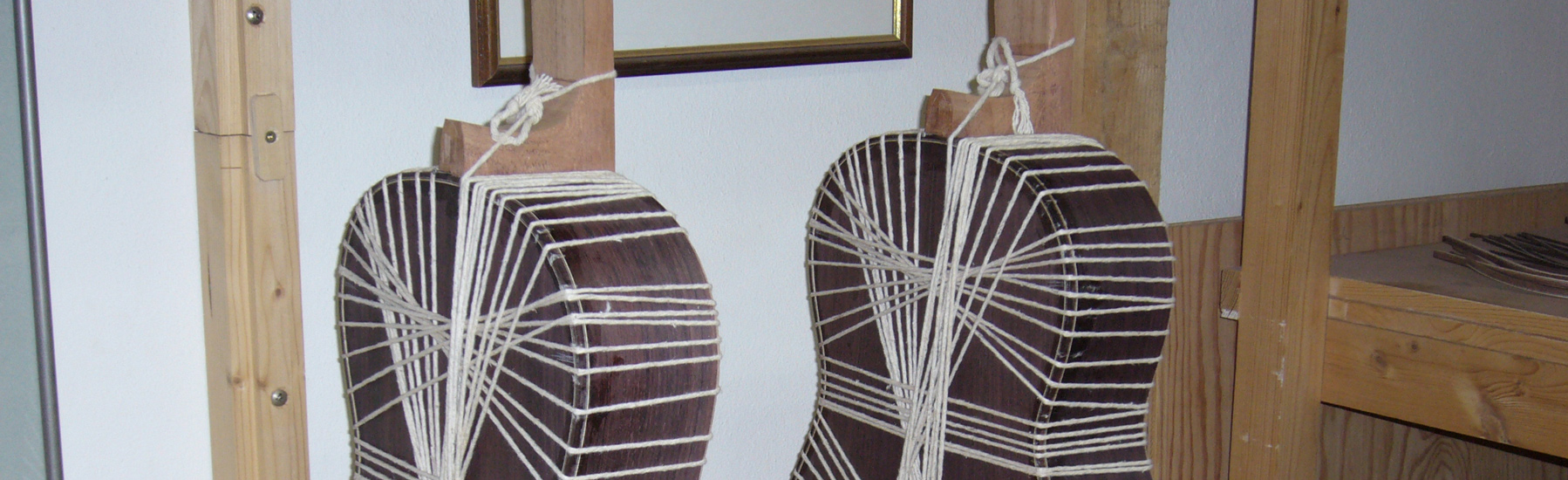